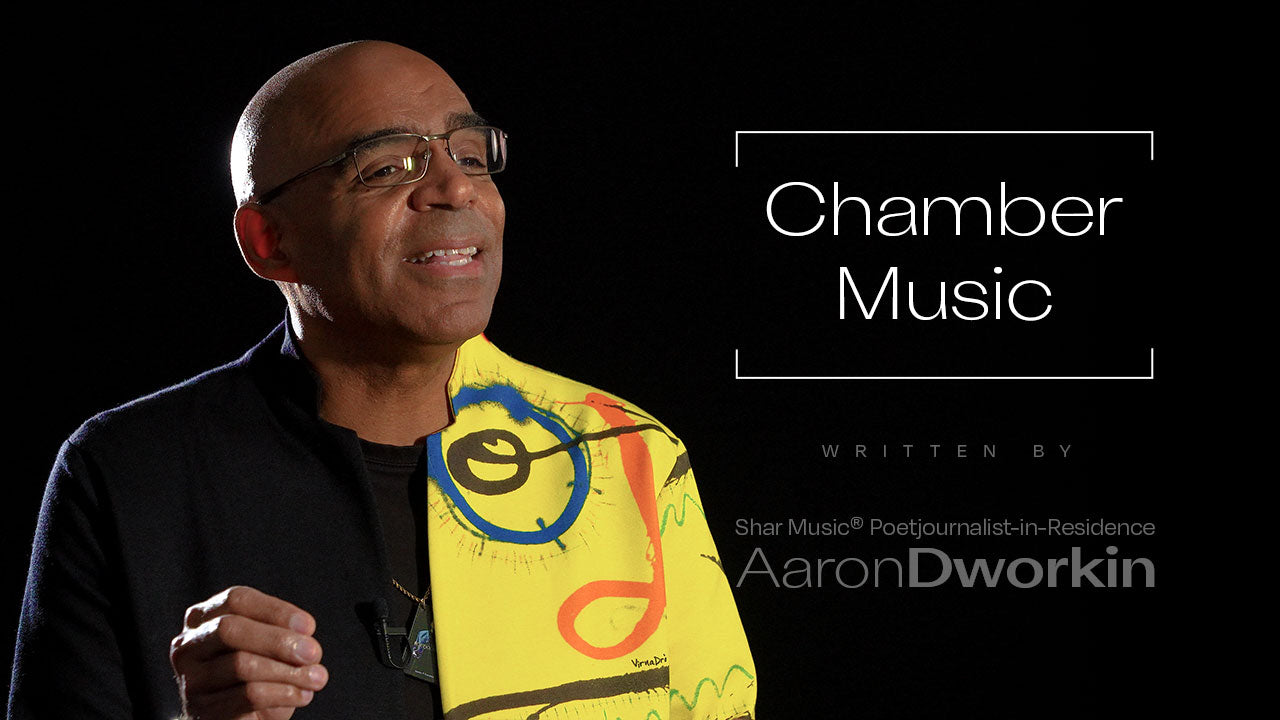
Poetjournalist-in-Residence
Aaron Dworkin's "Chamber Music"
Please enjoy Aaron Dworkin's newest work titled Chamber Music, which dives into the unique dialogue that occurs between instruments and the joy found in the shared art of creation.
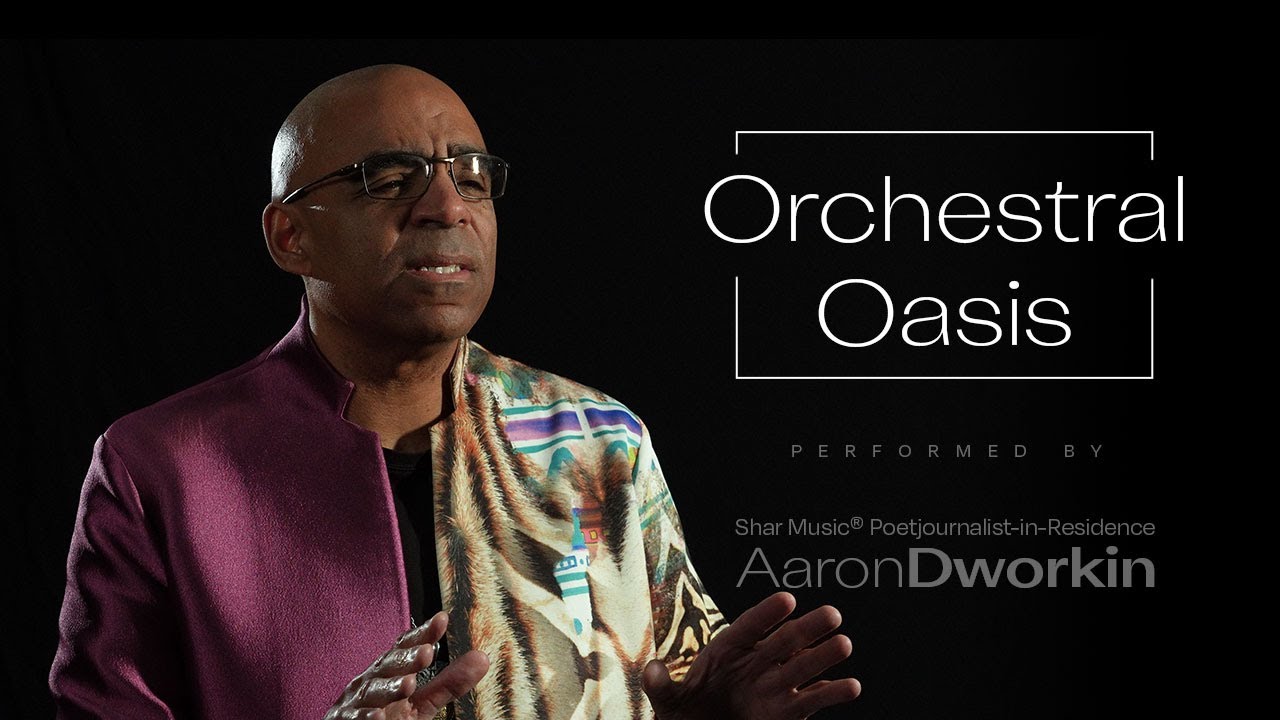
Poetjournalist-in-Residence
Aaron Dworkin's "Orchestral Oasis"
In tandem with Shar Music®, Aaron has created a group of poems that relate to classical music, his own life and experience, and the universal process of making art. Aaron Dworkin is a Poetjournalist, Social Entrepreneur, Performing Artist, Author, Filmmaker, Philanthropist, and Professor of Arts Leadership & Entrepreneurship at the University of Michigan School of Music, Theatre & Dance. In the weeks ahead, we’ll be sharing Aaron's poetry frequently on our Shar Music® Blog, our YouTube Channel and our Social Media accounts, so be sure to stay tuned!
Follow Shar Music: Instagram: https://www.instagram.com/sharmusic_/
Facebook: https://www.facebook.com/SharMusic
TikTok: https://www.tiktok.com/@shar_music
Pinterest: https://www.pinterest.com/sharmusic/
Twitter: https://twitter.com/SharMusic_
___________________
ABOUT:
Aaron Dworkin is a MacArthur “Genius” Fellow and was President Obama’s first appointment to the National Council on the Arts.; he is a current Professor of Arts Leadership and Fellowship at the University of Michigan’s School of Music, Theatre & Dance, as well as the founder of the Sphinx Organization, a non-profit dedicated to the development of young Black and Latino classical musicians. He has recorded and collaborated with a diverse range of artists from around the world, including Yo-Yo Ma, Damien Sneed, Anna Deveare Smith, Damian Woetzel, and Lil Buck. He is a best-selling author and the writer of the poetry collection They Said I Wasn’t Really Black. https://www.aarondworkin.com/
ABOUT: Shar Music®
Founded by musicians, for musicians. Shar Music® is a market leader in North America, and your best source for violin family instruments – violin, viola, cello, and bass – as well as strings, bows, sheet music, cases, and accessories. Our focus and our mission: making music accessible to everyone.
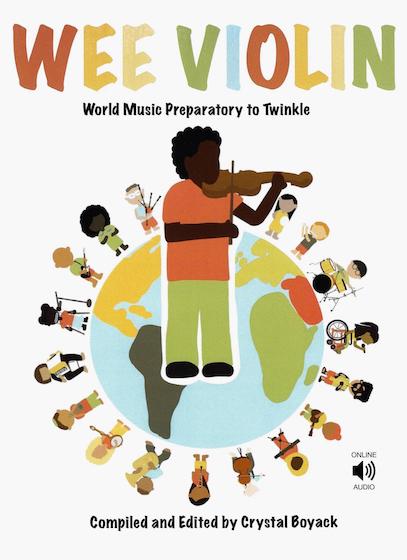
Educational Corner
Deep Diving into Crystal Boyack's "Wee Violin" Curriculum
Wee Violin is a collection of 33 traditional tunes from around the world that Boyack put together over a period of five years, designing a curriculum to support "Pre-Twinkle" beginners ages three through seven.
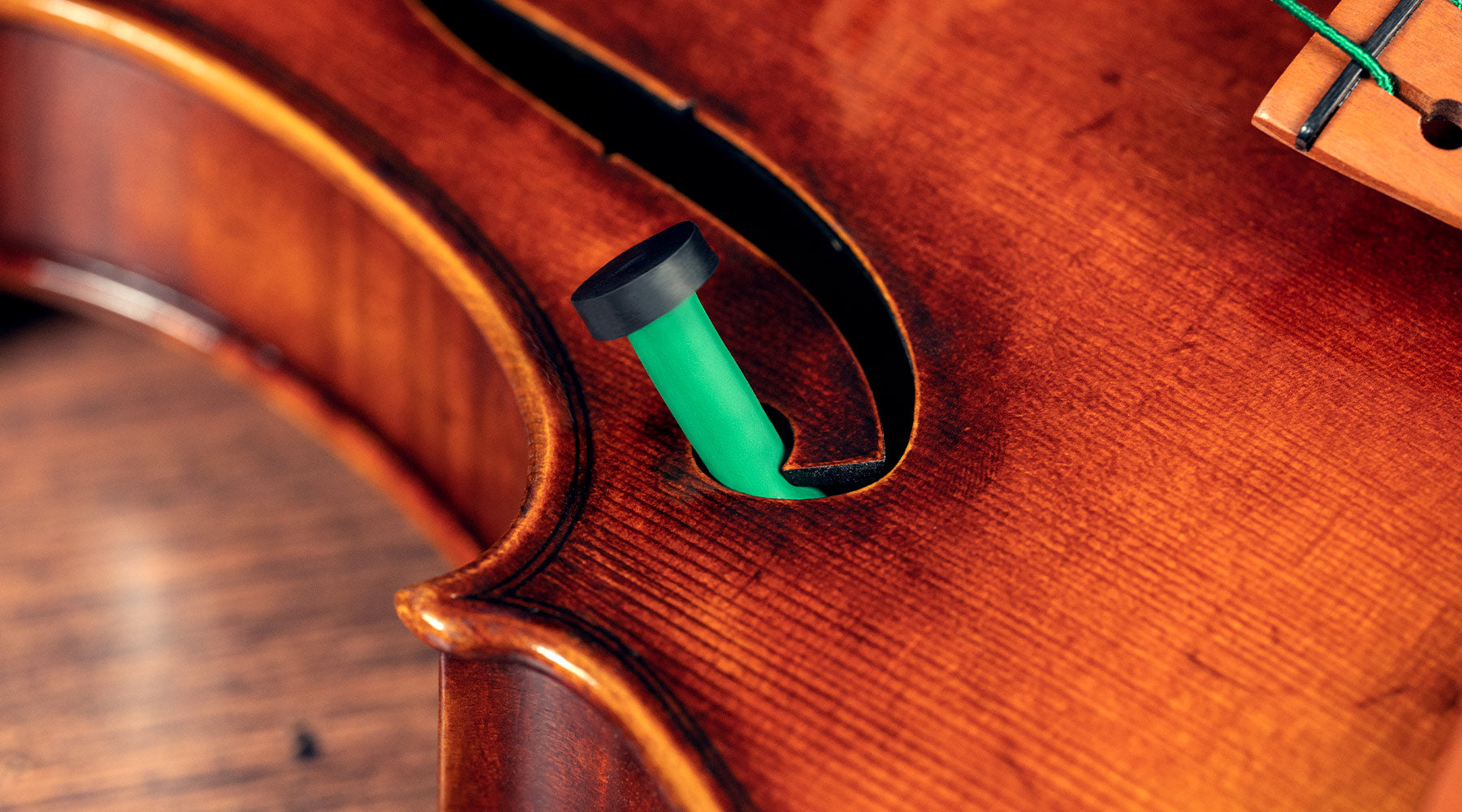
Educational Corner
With Cold Weather Comes Great Responsibility: A Guide to Humidification
As the weather gets colder, make sure you're thinking about instrument humidification to prevent any cracks or open seams. Follow along as we look into the various humidification systems available.
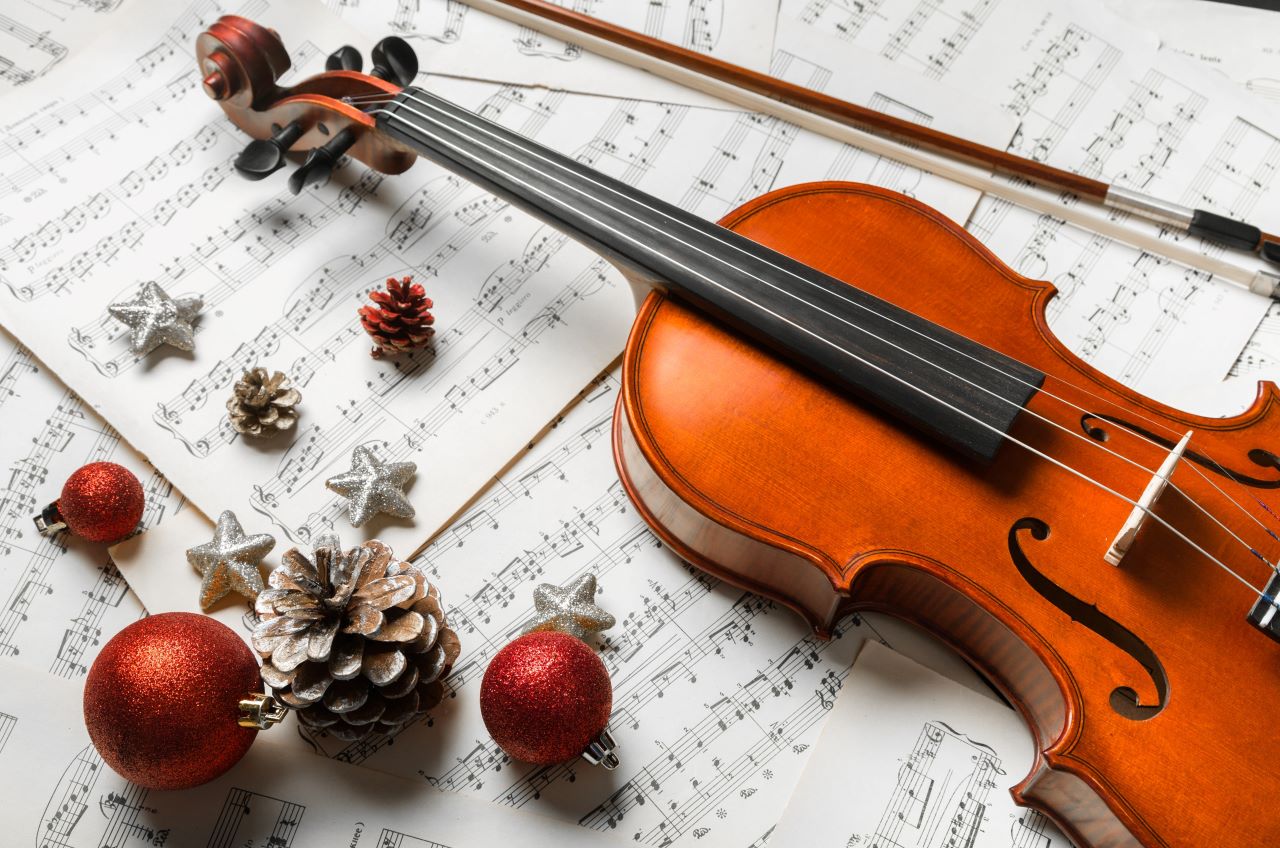
Pop Culture & Lifestyle
Perfect Gifts for the Suzuki Student (And Their Parents!)
Suzuki Students are some of the most hardworking and disciplined little string players out there. Here are a few gift ideas to help show your love for the Suzuki Student in your life this holiday season.
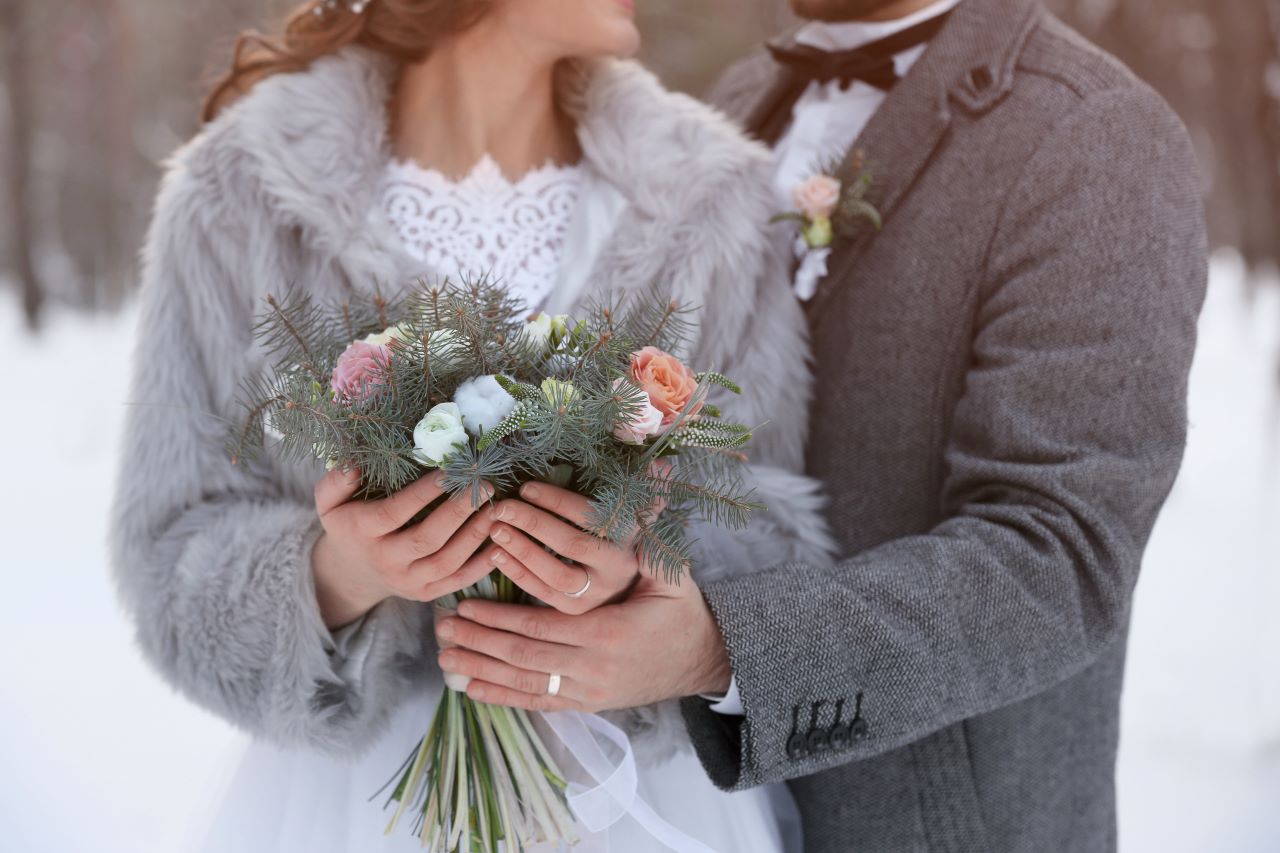
Fun & Entertainment
5 Popular Songs for a Winter Wedding—and 5 Unconventional Ones to Try
For more adventurous couples, the winter time and the holiday season can make for a magical wedding. For players, this means that a more creative approach to your wedding repertoire can make the ceremony and reception stand on its own against any holiday.
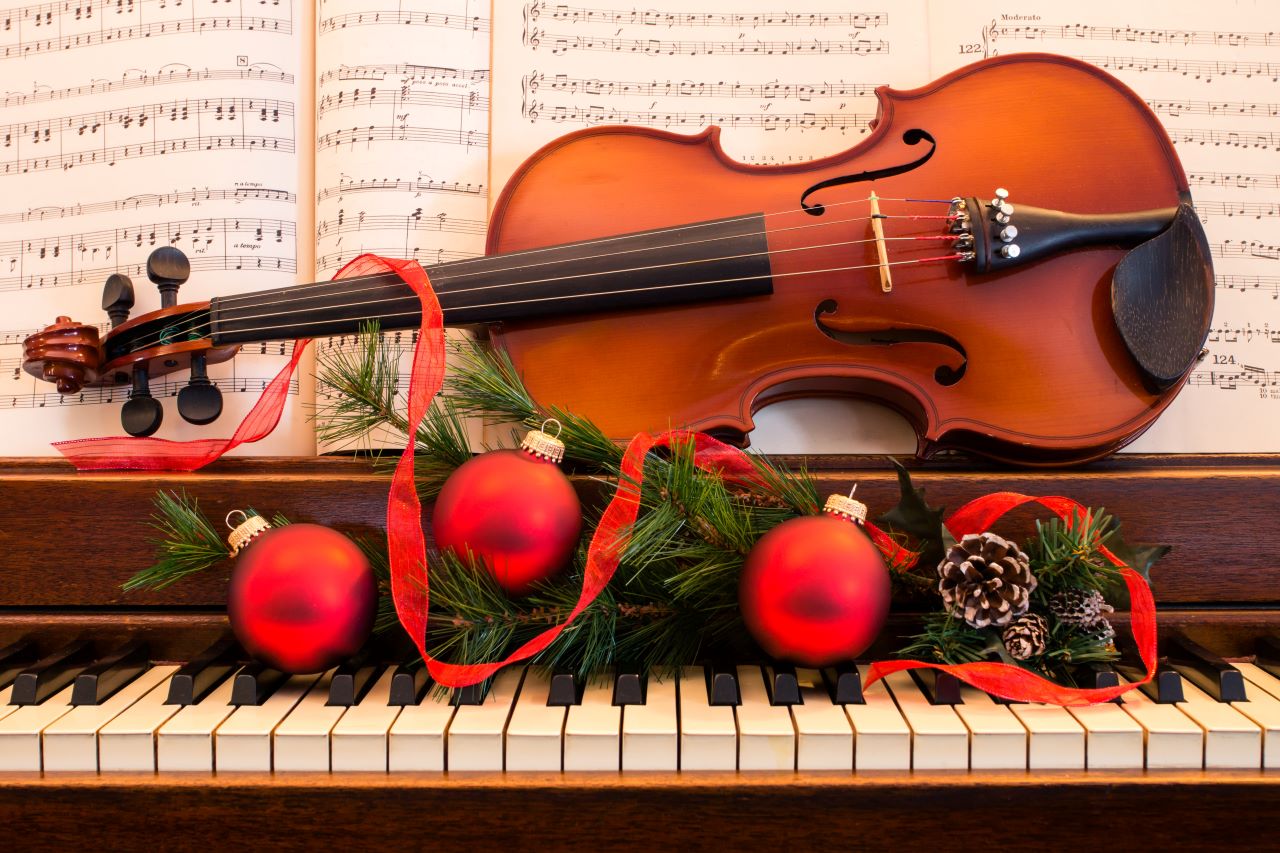
Fun & Entertainment
Gift Ideas to Celebrate the Teacher in Your Life
Teachers spend so much time with us, and for many string students that means for a large part of our lives. Here's how to show your appreciation for a teacher this year, whether you are a student or parent looking to show your support.

Poetjournalist-in-Residence
Aaron Dworkin's "Practice, Practice, Practice"
This month's poem is all about practice: the importance of routine, the serenity of solitude, the celebration of commitment to your craft.

Product Reviews
Eloise Hellyer on the Principles of Teaching Music
If you are interested in becoming a teacher, are a teacher yourself, or you want to learn more about how a teacher approaches violin pedagogy, 1 Teaches 2 Learn is for you.